Additive manufacturing (AM) of metals offers highest production flexibility, almost unlimited freedom of design and the potential for pointwise control of microstructure and mechanical properties. However, a sub-optimal choice of process parameters often leads to high residual stresses, dimensional warping, porosity, undesirable microstructures or even failure of the part during production. The main objective of this course is to convey the physical fundamentals of metal AM processes, the basics of process implementation and monitoring, material aspects as well as modeling and simulation techniques on different length scales.
The course begins with an overview of existing metal AM processes comprising powder bed fusion additive manufacturing (PBFAM), e.g. selective laser melting (SLM), selective laser sintering (SLS), electron beam melting (EBM), directed energy deposition (DED), binder jetting (BJ), and material droplet printing (MDP). After conveying the physical fundamentals, potential fields of application and the technical implementation, means of monitoring and process control are presented. Different types of defects in metal AM are categorized and strategies for defect detection via in-situ and ex-situ metrology (e.g. X-Ray computer tomography CT, density inspection, geometry control) are discussed. Moreover, the course will convey essential material aspects such as the principles, mechanisms and kinetics of solidification as well as the fundamentals of equilibrium and non-equilibrium thermodynamics. Phase formation and microstructure control, alloy design, powder metallurgy and process-microstructure-property correlations will be discussed in the context of metal AM and compared to conventional casting.
A further focus of the course lies on modelling and simulation approaches in metal AM, covering the underlying modelling assumptions, governing equations, discretization strategies as well as numerical aspects (e.g. balance of computational efficiency and solution accuracy). Specifically, modelling strategies for the mechanics, radiation transfer, heat transfer and sintering kinetics in powder beds are discussed. Moreover, mesoscale thermo-hydrodynamics modelling and simulation approaches aiming at the prediction of melt flow instabilities and final part properties such as surface roughness, layer-to-layer adhesion and residual porosity are conveyed. Eventually, part-scale thermo-solid-mechanics modelling and simulation approaches aiming at the prediction of residual stresses, thermal strains, constitutive behavior and dimensional warping at the length scale of entire design parts are presented.
Each set of lectures will start from the respective basics but will then quickly move on to cutting-edge research topics. The lectures are primarily designed for doctoral students of mechanics, engineering, material sciences and physics with a strong interest in the different research aspects of metal AM. However, they are equally suited for young and senior researchers, who would like to gain a comprehensive overview in an efficient compact course format. It might also be interesting for practicing engineers working on high-level industrial applications of metal AM.
Meier, C., Penny, R., Zou, Y., Gibbs, J.S., Hart, A.J.: Thermophysical phenomena in metal additive manufacturing by selective laser melting: Fundamentals, modeling, simulation and experimentation, Annual Review of Heat Transfer, 20:241-316, 2017.
Grasso, M., Colosimo, B.M.: Process defects and in-situ monitoring methods in metal powder bed fusion: a review, Measurement Science and Technology, 28:1-25, 2017.
DebRoy, T., Wei, H.L., Zuback, J.S., Mukherjee, T., Elmer, J.W., Milewski, J.O., Beese, A.M., Wilson-Heid, A., De, A., Zhang, W.: Additive manufacturing of metallic components - process, structure and properties. Progress in Materials Science, 92:112–224, 2018.
Gusarov, A.V., Smurov, I.: Modeling the interaction of laser radiation with powder bed at selective laser melting, Physics Procedia 5:381, 2010.
Hodge, N.E., Ferencz, R.M., Solberg, J.M.: Implementation of a thermomechanical model for the simulation of selective laser melting, Computational Mechanics, 54:33-51, 2014.
Meier, C., Weißbach, R., Weinberg, J., Wall, W.A., Hart, A.J.: Critical influences of particle size and adhesion on the powder layer uniformity in metal additive manufacturing, Journal of Materials Processing Technology, 266, 484-501, 2019.
5 lectures on: types of defects in metal AM; in-situ sensing (types of sensors and possible applications); ex-situ sensing (X-Ray CT, density inspection, control of geometrical specifications); application of data-driven approaches (e.g. machine learning) and uncertainty quantification in the context of AM process monitoring and control.
6 lectures on: metallurgical aspects of metal AM covering the principles, mechanisms and kinetics of solidification; equilibrium and non-equilibrium thermodynamics; phase formation and microstructure control; alloy design for metal AM; processing-microstructure-property correlations of AM parts; properties of AM parts in comparison with conventional casting; aspects of powder metallurgy.
5 lectures on: modeling of radiative transfer in powder beds; modeling of heat transfer in powder beds; experimental characterization of radiation and heat transfer in powder beds; coupled heat transfer and sintering kinetics in selective laser sintering; evaporation and induced gas-phase flows in selective laser melting.
6 lectures on: physical fundamentals, technical implementation and possible applications of the metal AM processes selective laser melting (SLM), selective laser sintering (SLS), electron beam melting (EBM), directed energy deposition (DED), binder jetting (BJ), and material droplet printing (MDP).
5 lectures on: physical effects relevant for part-scale thermo-solid-mechanics in metal AM; modeling techniques and numerical methods; efficiency and accuracy of numerical models; prediction of residual stresses and dimensional warping; constitutive modeling; outlook on coupled / wholistic modeling approaches.
6 lectures on: formulation and calibration of cohesive powder models; prediction of powder layer characteristics via powder recoating simulations; physical effects governing the melt pool thermo-hydrodynamics in metal AM; modeling techniques, numerical methods, efficiency and accuracy of melt pool models; prediction of surface quality, pores and defects via melt pool simulations.
The registration fee are:
- Participation in presence, 600.00 Euro + VAT*
This fee includes a complimentary bag, four fixed menu buffet lunches (on Friday upon request), hot beverages, download- able lecture notes.
- Participation online, 250.00 Euro + VAT*
This fee includes downloadable lecture notes.
Applicants must apply by September 18th for the "on-site" participation, and by October 11th for the "on-line" participation. Application forms should be sent on-line through the following web site: http://www.cism.it. A message of confirmation will be sent to accepted participants. Applicants requiring assistance with the registration should contact the secretariat at the following email address cism@cism.it.
Applicants may cancel their course registration and receive a full refund by notifying CISM Secretariat in writing (by email to cism@cism.it) no later than two weeks prior to the start of the course.
Cancellation requests received during the two weeks prior to the start of the course will be charged a 50.00 Euro handling fee. Incorrect payments are also subject to a 50.00 Euro handling fee.
A limited number of participants from universities and research centres who are not supported by their own institutions can be offered lodging and/or board, if available, in a reasonably priced hotel or student guest house.
Requests should be sent to CISM Secretariat by August 18, 2021 along with the applicant's curriculum and a letter of recommendation by the head of the department or a supervisor confirming that the institute cannot provide funding. Preference will be given to applicants from countries that sponsor CISM.
Information about travel and accommodation is available on the web site www.cism.it, or can be mailed upon request.
* where applicable (bank charges are not included), Italian VAT is 22%.
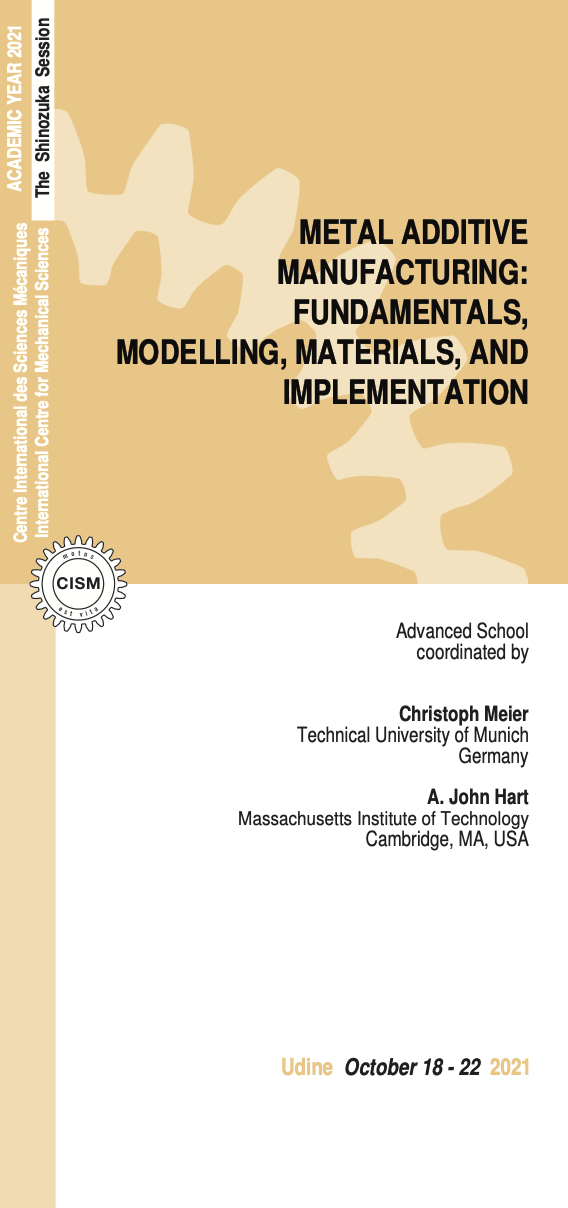