A central topic in mechanics consists in building “virtual laboratories” to optimize heterogeneous materials so as to achieve specific targets. This requires building constitutive models on one or more scales, devising and verifying wellsuited numerical schemes to solve the resulting mathematical problems numerically and, most importantly, to design and optimize experimental techniques to ensure the observability of relevant quantities, and validate the models.
Materials are heterogeneous or even discrete at some scale. Those heterogeneities can be accounted for either by averaging properties at smaller scales, or by considering explicitly the micro/meso structures of the materials. However, when failure occurs, it is no longer possible to separate micro from macro effects and more advanced strategies are required, such as error-controlled adaptive model order reduction or adaptive hybrid multi-scale methods.
Discretising the heterogeneities, cracks, dislocations and defects can be cumbersome using standard finite element methods (FEM). Enrichment and implicit boundary strategies can be applied to deal with complex and evolving boundaries/geometries, whereas other approaches aim at completely abolishing the need for finite element meshes. This class of mesh-free methods can be particularly appealing, since fullfield monitoring techniques typically measure data on scattered sets of points that can be directly used for simulation purposes. Sharing some appealing properties with mesh free methods, isogeometric methods were recently introduced with the aim to simplify the design-through analysis concept and were recently used for digital image correlation. Such full-field techniques, used to measure material deformation, have brought up a revolution in mechanical testing of materials.
The visualisation of deformation maps enables researchers to naturally address heterogeneities. In particular, the Digital Image Correlation (DIC) and grid-based methods are particularly appealing thanks to their simplicity and reasonably low cost. There are also techniques to measure deformation in the bulk of materials, such as Digital Volume Correlation (DVC).
The identification of material parameters from such full-field kinematic measurements can be done using finite element model updating for material parameter identification. An alternative technique called the Virtual Fields Method (VFM) relies on global equilibrium equations and efficiently deals with parameter identification of non-linear constitutive laws or heterogeneous materials. Furthermore, this approach relaxes strong constraints on specimen shape and load, opening the possibility of a very large design space for novel experimental procedures.
The course will include carefully crafted presentations covering in detail all these aspects, providing a comprehensive overarching framework for experimental, numerical and theoretical mechanics of heterogeneous materials. After the course the participant will be able to:
(1) select suitable models, implement discretisation techniques and solution algorithms for nonlinear multi-scale problems for heterogeneous materials;
(2) verify the numerical methods and validate the material models by a combination of a posteriori error estimation and advanced experimental techniques for heterogeneous materials;
(3) develop and optimise suitable experimental techniques to observe phenomena of interest, identify material properties and characterise heterogeneous materials.
The course is addressed to doctoral students and postdoctoral researchers in mechanical, civil, material science, applied physics and applied mathematics, academic and industrial researchers.
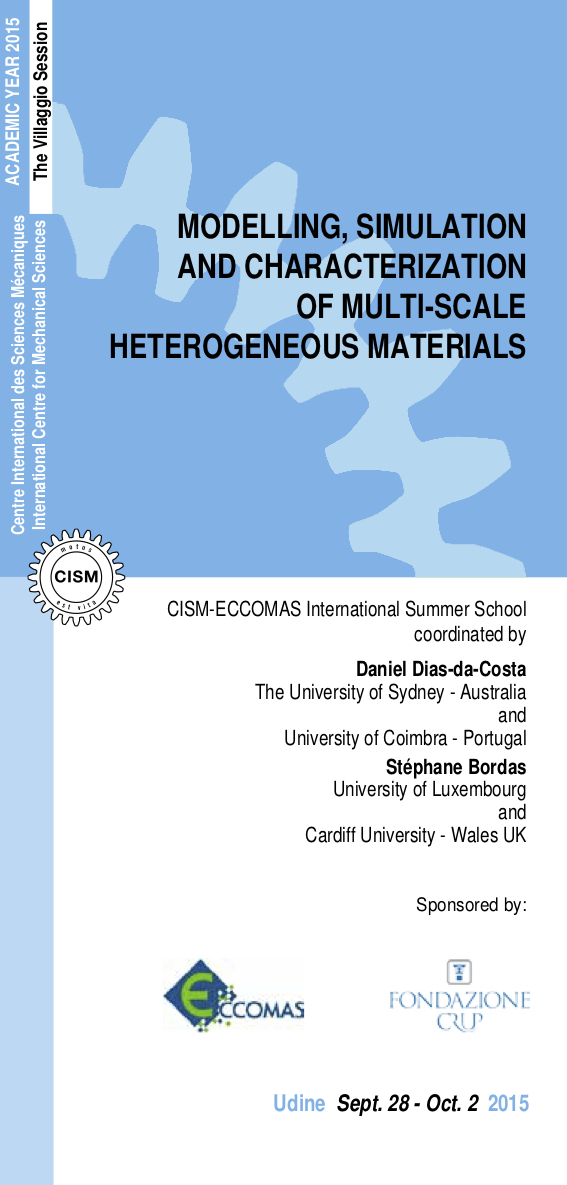