Dynamics of metal cutting is a relevant research topic that has an essential theoretical background both in mechanics of solids and in dynamics of rigid bodies. The basic difficulty was summarized as early as 1907 by F. W. Taylor, the 3rd president of ASME:
“… Chatter is the most obscure and delicate of all problems facing the machinist – probably no rules or formulae can be devised which will accurately guide the machinist in taking maximum cuts and speeds possible without producing chatter…”
Chatter refers to the vibrations that may arise during cutting processes. This specific self-excited oscillation is mainly caused by the so-called regenerative effect. The undesired relative vibrations between the tool and the work-piece deteriorate the quality of machined surfaces. If the modal parameters, like natural frequencies, damping, vibration modes, are identified on a machine tool, and if the cutting force is estimated by means of well-established cutting mechanics models, then there is a chance to predict and to prevent chatter by selecting appropriate cutting parameters (feed rate, depth of cut and cutting speed) and achieve maximal material removal rates. During the last 100 years, the research methodology has developed parallel to the theoretical and numerical methods in mathematics, informatics, vibration theory, measurement techniques and nonlinear dynamics including chaos.
The advanced course provides a full spectrum of the research results in machining dynamics from the theoretical background of nonlinear delayed oscillators to the practical issues of modal testing. Mechanical and mathematical models are presented both in frequency domain and in time domain. Introduction is given to advanced numerical and software solutions to carry out virtual machining to optimize cutting parameters. The hardware-in-the-loop technique is introduced for enhanced design of improved tool geometries. Optimization of milling tool geometry (pitch and helix angles) is discussed. Methods involving partial modification of the machine tool structure are also presented, like the various dynamic vibration absorbers. Up-to-date experimental modal testing methods and their future development strategies are overviewed together with the sophisticated construction of the stability charts that are relevant for industrial applications. Research and commercial solutions for real-time chatter detection and process regulation are discussed. An industrial panel will bridge the state-of-the-art research results and actual industrial needs in machining dynamics.
The school is addressed to doctoral students, post-docs, early career researchers and engineers working at R&D departments of companies with interest in improving machining efficiency. The course is designed for participants working in the field of dynamics of machining and related topics like deep drilling, also to those interested in vibration measurement techniques, hardware-in-the-loop applications and/or in other fields of dynamics of delayed oscillators from traffic dynamics to human-machine systems in general.

Altintas Y, Manufacturing automation: metal cutting mechanics, machine tool vibrations, and CNC design. Cambridge University Press, Cambridge, 2012.
Stepan G, Modelling non-linear regenerative effects in metal cutting, Philosophical Transactions of the Royal Society 359 (2001) 739-757.
Veraszto Z, Stepan G, Nonlinear dynamics of hardware-in-the-loop experiments on stick–slip phenomena, Int. Journal of Non-Linear Mechanics 94 (2017) 380–391.
Azvar M, Budak E, Multi-Dimensional Chatter Stability for Enhanced Productivity in Different Parallel Turning Strategies, Int. Journal of Machine Tools and Manufacture, Vol. 123, pp. 116-128, 2017.
Comak, A. and Budak, E., Modeling Dynamics and Stability of Variable Pitch and Helix Milling Tools for Development of a Design Method to Maximize Chatter Stability, Precision Engineering, 47 (2017) 459-468.
Tunc LT, Budak E, Effect of Cutting Conditions and Tool Geometry on Process Damping in Machining, International Journal of Machine Tools and Manufacture, Vol. 57, pp.10-19, 2012.
Munoa J, Beudaert X, Dombovari Z, Altintas Y, Budak E, Brecher C, Stepan G, Chatter suppression techniques in metal cutting, CIRP Annals – Manufacturing Technology 65 (2016) 785-808.
Munoa J, Beudaert X, Erkorkmaz K, Iglesias A, Barrios A, Zatarain M, Active suppression of structural chatter vibrations using machine drives and accelerometers, CIRP Annals-Manufacturing Technology, 64/1 (2015) 385-388.
Ewins, DJ, Modal Testing: Theory and Practice, and Application, Research Studies Press, 2000.
Dombovari Z, Dominant Modal Decomposition Method, Journal of Sound and Vibration, 392 (2017) 56-69.
Sortino M, Totis G, Prediction and Control of Vibrations and Chatter in Machining, chapter in: Mechatronics: principles, technologies and applications (Ed: Brusa E) Nova Science Pub Inc, New York, 2015.
Kuljanic E, Sortino M, Totis G, Multisensor Approaches for Chatter Detection in Milling, Journal of Sound and Vibration, 312 (2008) 672-693.
6 lectures on: mechanics of metal cutting; chip generation mechanism for two dimensional orthogonal cutting, and three dimensional operations like milling, drilling and turning; modeling dynamics of the machining-machine tool structure, cutting process stability in frequency domain; physics-based virtual machining system; selecting depth of cut, feed and speed for optimal tool path generation.
6 lectures on: machine tool dynamics with special emphasis on spindle and tooling; effects of machine tool and workpiece dynamics on process stability; optimal design of variable pitch and helix milling tools for improved stability; identification and modeling of process damping, demonstration with real-world applications; dynamics and stability of parallel machining and micro milling systems.
6 lectures on: modal analysis of multiple DoF mechanical systems; tools and methods of modal testing; extraction of conventional modal parameters; dynamic models based on results of experimental modal analysis; modelling dynamic systems by Green function representation; theoretical background and application of Receptance Coupling Substructure Analysis; examples for machine tool structures.
6 lectures on: factors affecting chatter: workpiece material, cutting parameters, tool geometry, dynamic stiffness of structure; chatter suppression methods for industrial applications; guideline for the selection of most suitable techniques; application of special tool geometries, spindle variation techniques, passive damping techniques and active dampers for chatter elimination.
6 lectures on: modeling machine tool vibrations in time domain; time dependent delay equations for turning and milling, state dependent delays; relevant nonlinearities in the tool/workpiece interaction; regenerative vibrations, chatter, stability charts, bifurcations; design of Hardware-in-the-Loop (HIL) experiments; development of advanced cutting tools.
5 lectures and industrial panel on: selection of tooling system characteristics and cutting parameters; upgraded models of milling dynamics and the symmetry breaking effects; computational efficiency of alternative chatter prediction algorithms; effects of model parameter uncertainties on stability; chatter detection systems; advanced signal processing and data fusion techniques for accurate and robust detection of chatter vibrations.
The registration fee is 600.00 Euro + VAT*, where applicable (bank charges are not included). The registration fee includes a complimentary bag, four fixed menu buffet lunches (on Friday upon request), hot beverages, downloadable lecture notes and wi-fi internet access.
Applicants must apply at least one month before the beginning of the course. Application forms should be sent on-line through the following web site: http://www.cism.it. A message of confirmation will be sent to accepted participants. Applicants requiring assistance with the registration should contact the secretariat at the following email address cism@cism.it.
Applicants may cancel their course registration and receive a full refund by notifying CISM Secretariat in writing (by email to cism@cism.it) no later than two weeks prior to the start of the course.
Cancellation requests received during the two weeks prior to the start of the course will be charged a 50.00 Euro handling fee. Incorrect payments are also subject to a 50.00 Euro handling fee.
A limited number of participants from universities and research centres who are not supported by their own institutions can be offered lodging and/or board, if available, in a reasonably priced hotel or student guest house.
Requests should be sent to CISM Secretariat by March 6, 2019 along with the applicant's curriculum and a letter of recommendation by the head of the department or a supervisor confirming that the institute cannot provide funding. Preference will be given to applicants from countries that sponsor CISM.
Information about travel and accommodation is available on the web site www.cism.it, or can be mailed upon request.
* Italian VAT is 22%.
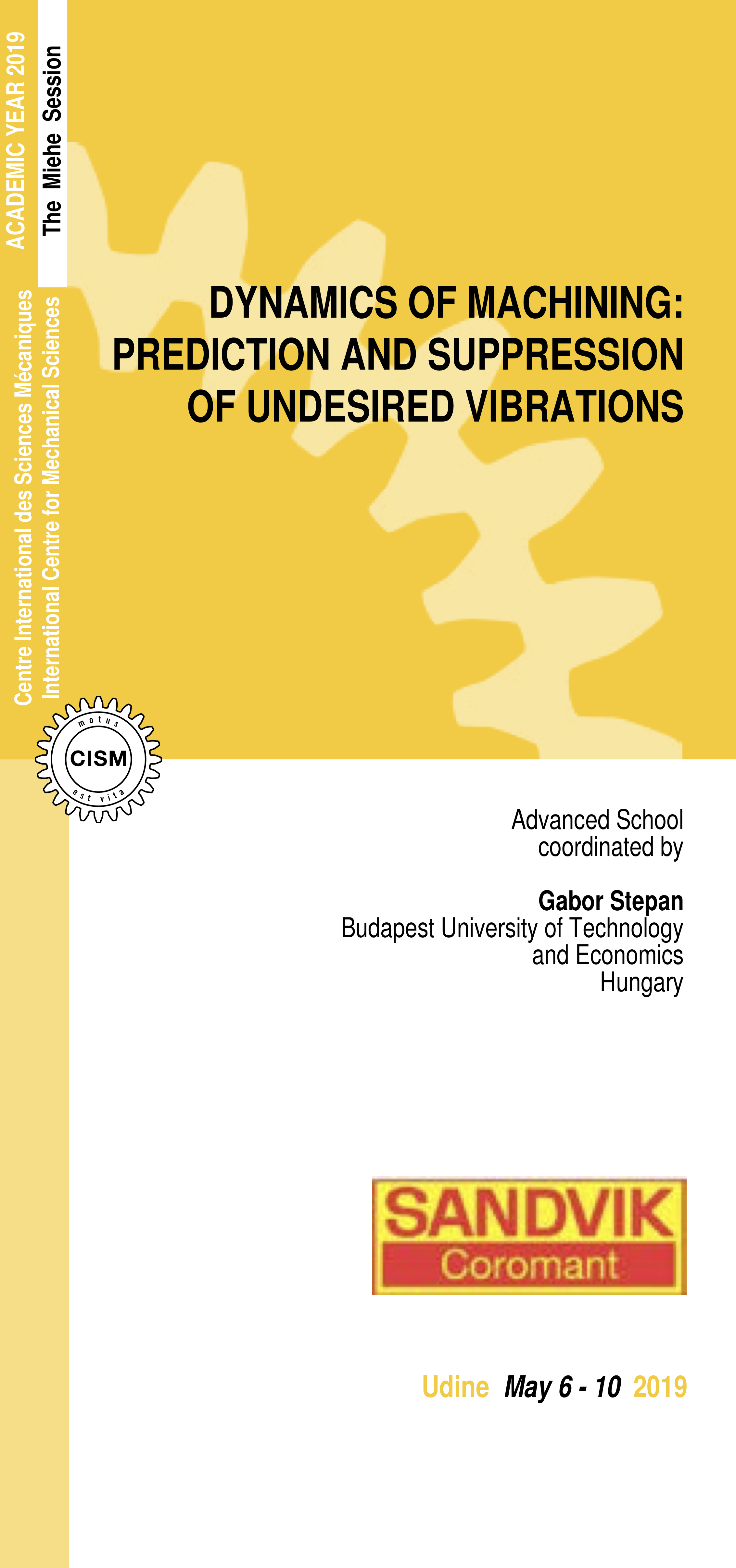