Because of its low cost and outstanding properties, steel is by far the most common and versatile material, with a wide range of applications such as in mechanical, civil and architectural engineering. With numerous combinations of alloying elements and microstructures, the spectrum of achievable mechanical properties, e.g., strength, ductility, toughness and durability, is unparalleled. However, the production of steel is not environmentally friendly due to the large amounts of carbon dioxide generated by the inherent reduction of iron oxide by carbon. New processes, such as hydrogen reduction, and better recycling solutions are at different stages of research but will take decades before full implementation and production.
Nevertheless, to reduce the impact of steel on the environment, much progress can be achieved in the near future through the optimization of steel products, which is the focus of this course. The mechanical properties of steel are dominated by its elasto-viscoplastic behavior and limited by its fracture modes. Since the plastic behavior is highly sensitive to the material considered, and fracture even more, it is impossible to synthetize the broad diversity of mechanical responses in just a few scenarios but there are some commonalities within the steel family as well as with other metals. In addition, these aspects highly depend on the manufacturing processes and service conditions of the products, in particular temperature.
Because product design optimization relies ever more on numerical simulations, it is essential to develop modeling techniques that account for the important aspects above. The solutions of a boundary value (BV) problem, whether a forming process or the fatigue behavior of a structural component, is guided by the laws of mechanics and numerically obtained by discretization of space and time, generally through finite element (FE) analyses. For better time efficiency, only a discrete number of finite element simulations with limited sets of process or performance parameters may be executed, the results of which providing the necessary data to train a neural network. Subsequently, this meta-model is employed to provide the simulation result of a complex BV problem in seconds for any interpolated set of parameters, which renders an optimization very simple and time-efficient to conduct. It is clear that the accuracy of the FE model, which may be used directly or provide the input for the meta-model based on neural network, is essential for the success of an optimization procedure. This is the reason why the relationships between stress, strain and other variables, i.e., the constitutive description, must be as accurate as possible. The plastic behavior must be experimentally characterized accurately and represented by constitutive equations. Although a number of failure mechanisms result directly from the solution of such BV problem, others such as fracture are not predictable without specific criteria as well as specific implementations into numerical tools. Therefore, the objective of this course is to demonstrate the importance of the description of the constitutive and fracture modeling of steel and other selected metals with applications to forming, cyclic loading and fatigue, crack propagation and toughness. Although many of these models are developed at a continuum mechanics scale, they are based on the understanding of deformation mechanisms. Moreover, this course underline that modern identification approaches of the mechanical behavior such as the virtual fields method, which is particularly suitable for constitutive model calibration, are introduced. Finally, since temperature is an important variable, specific aspects relevant to the resistance to high temperature creep and the cryogenic application of stainless steel to superconductors, are introduced.
Naumenko, K.; Altenbach, H. (2016): Modeling High Temperature Materials Behavior for Structural Analysis Part I: Continuum Mechanics Foundations and Constitutive Models, Cham: Springer, Advanced Structured Materials, vol. 28. ISBN: 978-3-319-31627-7, DOI: 10.1007/978-3-319-31629-1.
Naumenko, K.; Altenbach, H. (2020): Modeling High Temperature Materials Behavior for Structural Analysis Part II: Solution Procedures and Structural Analysis Examples, Cham: Springer, Advanced Structured Materials, vol. 112. ISBN: 978-3-030-20381-1, DOI: 10.1007/978-3-030-20381-8.
Bari, S. and Hassan, T., "An Advancement in Cyclic Plasticity Modeling for Multiaxial Ratcheting Simulation," International Journal of Plasticity, Vol. 18, pp. 873-894, 2002.
Krishna, S., Hassan, T., Naceur, I.B., Sai, K., Cailletaud, G., “Macro versus Micro Scale Cyclic Plasticity Models in Simulating Nonproportional Cyclic and Ratcheting Responses of Stainless Steel 304,” International Journal of Plasticity, Vol. 25, pp. 1910-1949, 2009.
Ahmed, R., Barrett, P.R., Hassan, T., Unified viscoplasticity modeling for isothermal low-cycle fatigue and fatigue-creep stress-strain responses of Haynes 230, International Journal of Solids and Structures, 88-89, 131- 145, 2016.
A. Pineau, T. Pardoen, A.A. Benzerga, Failure of metals – I. Brittle and ductile fracture, Acta Materialia 107 (2016) 424-483.
Grédiac, M., Hild, F., Full-field mea- surements and identification in solid mechanics. John Wiley & Sons, 2012.
Lattanzi, A., Barlat, F., Pierron, F., Marek, A., & Rossi, M. (2020). Inverse identification strategies for the characterization of transformation-based anisotropic plasticity models with the non-linear FM. International Journal of Mechanical Sciences, 173, 105422.
J. Tabin, B. Skoczen, J. Bielski, 2019. Discontinuous plastic flow coupled with strain induced fcc–bcc phase transformation at extremely low temperatures, Mechanics of Materials 129, 23 - 40.
Barlat, F., Yoon, S.Y., 2022. Anisotropic Plasticity during Non- Proportional Loading. Course and Lectures at the International Center for Mechanical Sciences (CISM), Udine, Italy, 2021. Altenbach, H., Ganczarski, A., Eds., Springer, in press.
6 lectures on: Creep at Elevated Temperatures
Creep and other types of time-dependent behavior, Phenomenological Models, Creep constitutive Equations Based on Rheological Models, Applications, Extension to other Materials.
6 lectures on: Plasticity and Forming
Modeling of strain path-dependent plasticity using continuum theories. Applications to pressure-dependent stress-strain behavior of advanced high strength steels subject to reversals and cross-loading effects.
6 lectures on: Cyclic loading and fatigue
Cyclic plasticity responses of various alloys; Classical plasticity theories; Non-linear kinematic hardening rate-independent model; Non-linear kinematic hardening viscoplasticity model.
6 lectures on: Micromechanics of ductile fracture and crack propaga- tion
Different mechanisms of nucleation, growth and coalescence of voids in modern steel for homogenous and cracked conditions. Experimen- tal and modelling techniques. Predictive models of ductile fracture and cracking that directly relies on a micromechanical description of physical phenomena.
6 lectures on: Advanced methods for the calibration of complex plasticity models
Introduction to inverse methods for material characterization with finite element model updating and the virtual fields method in plasticity. Design of specimens and development of experimental strategies for material behavior information enrichment.
6 lectures on: The elasto-plastic behaviour and fracture of steels at extremely low temperatures
Phenomena that occur in stainless steels in liquid or superfluid helium near 0K, intermittent plastic flow, plastic strain induced fcc-bcc phase transformation. Evolution of micro-damage and macrocrack propa- gation in metastable steels at extremely low temperatures. Multiscale constitutive models of related physical phenomena.
The course is offered in a hybrid format giving the possibility to attend the course also by remote (on Microsoft Teams platform). On-site places are limited and assigned on first come first served basis.
The registration fees are:
- On-site participation, 600.00 Euro + VAT*
This fee includes a complimentary bag, five fixed menu buffet lunches, hot beverages, downloadable lecture notes.
Deadline for on-site application is August 26, 2022.
- Online participation, 250.00 Euro + VAT*
This fee includes downloadable lecture notes. Deadline for online application is September 14, 2022.
Application forms should be sent on-line through the following web site: http://www.cism.it
A message of confirmation will be sent to accepted participants.
Upon request a limited number of on-site participants can be accommodated at CISM Guest House at the price of 30 Euro per person/night (mail to: foresteria@cism.it).
* where applicable (bank charges are not included) Italian VAT is 22%.
CANCELLATION POLICY
Applicants may cancel their registration and receive a full refund by notifying CISM Secretariat in writing (by email) no later than:
- August 26, 2022 for on-site participants (no refund after the deadline);
- September 14, 2022 for online participants (no refund after the deadline).
Cancellation requests received after these deadlines will be charged a 50.00 Euro handling fee. Incorrect payments are subject to Euro 50,00 handling fee.
GRANTS
A limited number of participants from universities and research centres who are not supported by their own institutions can request the waive of the registration fee and/or free lodging.
Requests should be sent to CISM Secretariat by July 26, 2022 along with the applicant's curriculum and a letter of recommendation by the head of the department or a supervisor confirming that the institute cannot provide fund- ing. Preference will be given to applicants from countries that sponsor CISM.
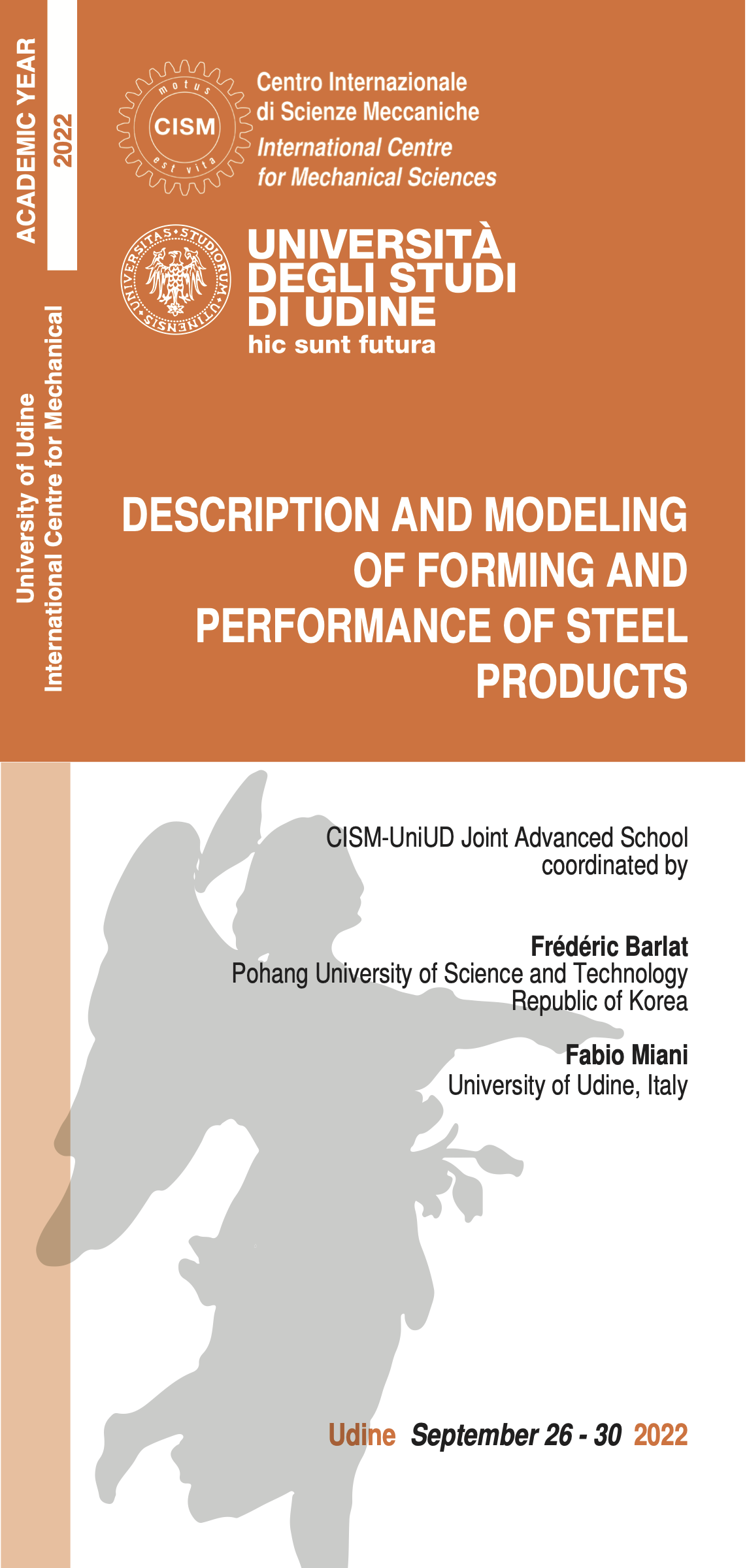