Welding is today the most common joining method for metallic structures. Its industrial application is extremely important and many of the large structures designed and erected in the last decades would not have been possible without modern welding technology. Typical examples are steel bridges, ship structures and large offshore structures for oil exploitation. The strength analysis of welded structures does not deviate much from that for other types of structures. Various failure mechanisms have to be avoided through appropriate design, choice of material and structural dimensions. Design criteria such as yielding, buckling, creep, corrosion and fatigue must be carefully checked for given loading conditions and environments. It is, however, a fact that welded joints are particularly vulnerable to fatigue damage when subjected to repetitive loading. Fatigue cracks may initiate and grow in the vicinity of the welds during service life even if the dynamic stresses are modest and well below the yield limit. The problem becomes very pronounced if the structure is optimized by the choice of high strength steel. The very reason for this choice is to allow for higher stresses and reduced dimensions, taking benefits of the high strength material with respect to the yield criterion. However, the fatigue strength of a welded joint is not primarily governed by the strength of the base material of the joining members; the governing parameters are mainly the global and local geometry of the joint. Hence, the yield stress is increased, but the fatigue strength does not improve significantly. This makes the fatigue criterion a major issue; the fatigue strength will alone give the requirements for the final dimensions of the structural members such as plates and stiffeners. To overlook this fact may result in fatigue facture and serious consequences. Objectives and scope of the presentation The presentation is confined to fusion welded steel structures and it covers the following subjects: · The basic understanding of the fatigue behaviour of welded joints based on theoretical considerations and experimental results. · The S-N approach with reference to current rules and regulations. · The fracture mechanics approach with numerical computations. · Reliability modelling and risk assessments. · Recent advances in understanding the fatigue process and estimating the fatigue life. Although the presentation emphasizes the practical aspects of fatigue life calculations and the assessment of crack growth and criticality, some advances in methods and models are included. The ultimate objective is to achieve optimized structures with respect to fatigue design, dimensions and inspection efforts without compromising reliability and safety. About the lecturer Professor Naman Recho was educated at the French University of Pierre and Marie Curie in Paris. He graduated in this university as Doctor Engineer in 1980 and “Docteur d’Etat Es-Sciences Physiques” in 1987. He is full Professor since 1988. From 1978 to 1988 he was with CTICM (Centre Technique Industriel de la Construction Métallique) in Paris. Between 1988 and 1993, he was Professor at the University of Haute Alsace in Mulhouse (France). Between 1993 and 2005 Naman Recho was Professor at the University Blaise Pascal in Clermont Ferrand, (France). He has written two textbooks within fracture mechanics. He has worked extensively with conceptual and applied aspects of fracture mechanics. In the recent 10 years, he participated into several research programs with industries such as (CETIM-Senlis, Bureau Veritas, Giat-Industrie, Michelin, CEA-Saclay, Trelleborg Industrie). Naman Recho founded in 1986 the program MMS (Mécanique des Matériaux et Structures) at EPF –Ecoles d’Ingénieurs in Sceaux near Paris. He is still managing this program. Since 1985 he has also been teaching at CHEC (Centre des Hautes Etudes de la Construction – Paris). He is "Guest Professor" at HUT (Hefei University of Technology in China). He is at present with CNRS (National Centre of Scientific Research) in Paris.
Recho, N. – Rupture par fissuration des structures, Hermes Sciences Publications, 1995. Lassen, T.; Recho, N. – Fatigue Life Analyses of Welded Structures, ISTE Publishing Company; 1st edition to appear in July 2006.
Naman Recho (None)
I- CRACK PROPAGATION I-1- Brittle Fracture I-2- Crack Bifurcation I-3- Fatigue Crack Propagation I-4- Experimental Aspects of Rupture and Crack Propagation II- FRACTURE MECHANICS MODELLING OF WELDED PLATES - Calibration against Experimental Data - II-1- Fracture Mechanics Modelling of Fatigue II-2- Potential Use of Fracture Mechanics to Fatigue Design II-3-Crack Propagation by Fatigue of Welded Structures submitted to Complex Mechanical Environment III- RANDOM LOAD HISTORIES, CYCLE COUNTING, FATIGUE THRESHOLDS III-1- Different Random Load Histories and Cycle Counting III-2- Cumulation Problem and Fatigue Damage III-3- Overloads During Fatigue III-4- Fatigue design and reliability analysis of welded joints IV - INDUSTRIAL APPLICATION OF FATIGUE LIFE CALCULATION AND CRACK GROWTH IV-1- Overview of Industrial and Practical Cases of Application of the Above Presented Methods IV-2- Open Discussion and Final Remarks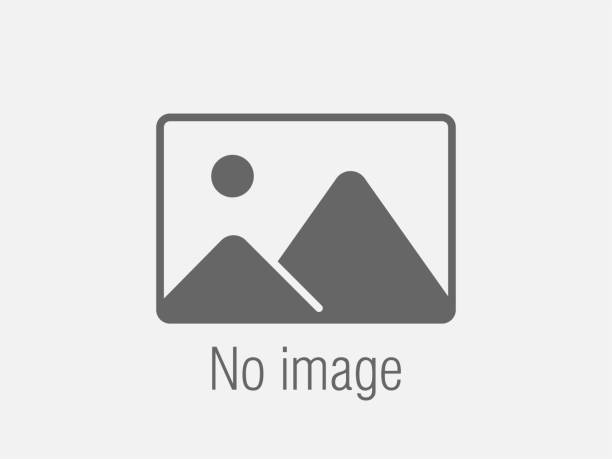