High reliability and reduced weight are, together with competitive costs, standard product requirements in mechanical engineering. At the same time, there is a demand for shorter product development cycles in order to reduce the time-to-market for new product ideas. The methods of fatigue analysis provide us with methods for fulfilling the contrasting requirements of lightweight design and increased reliability. An implementation of these methods in design, simulation and testing also increases the efficiency of the product development process. Failure of components in mechanical engineering may be caused by · forced rupture, · fatigue, · inadmissible defomation, · instability (creep, buckling), · wear, and · corrosion. There are only a few cases where the failure of mechanically loaded components is due to static overloads. Most components fail because of cyclic loads leading to material fatigue. The discipline of fatigue analysis develops methods for the prediction of the fatigue life of components. These methods are based on knowledge about · the stress distribution in the component, · the load spectra of the machine or its parts, and · the constitutive behaviour of the material under cyclic loading. For the determination of the stresses, numerical methods are widely used. Load spectra are mainly established by tests, for improvements of existing machines also from former experiences; in the case of new product developments, the spectra are derived from multi-body dynamics simulations. The third group of input data for the fatigue life prediction is the constitutive behaviour of the material, which is generally described by S/N curves based on fatigue tests on standard specimens. These S/N curves are not universally valid for a specific material; rather, they are influenced essentially by the type of loading, the presence of notches and stress concentrations within the component, the manufacturing process, the operating temperature etc.. Determining such a multitude of S/N-curves for a specific material by means of experiment is prohibitively expensive with respect to time as well as to costs; instead, the S/N curves may be synthetisized from simplified models that mirror correctly the underlying dependencies. Numerical simulation methods have become increasingly important in this field. Objectives and scope of the seminar Fatigue life calculations for geometrically complex structures require a detailed knowledge of the local fatigue behaviour of the material. Therefore, the emphasis of this seminar is put on models for generating S/N curves of components. These models are used in fatigue life analyses based on local stresses in order to account, among others, for geometrical effects in fatigue, such as the influence of stress concentrations and component size. Special emphasis will be put on technological influences stemming, e.g., from casting, forming, welding, and surface treatments. Further topics will cover the description of the low cycle (LCF) and thermo-mechanical (TMF) fatigue behaviour of components. About the lecturer Professor Wilfried Eichlseder obtained his higher education in mechanical engineering at the Technical University of Graz in Austria, where was awarded his diploma in 1980 and the PhD in 1989. In 1981 he started at Steyr-Daimler-Puch AG (now Magna-Steyr) as a finite element analyst within the research department. In this period he also developed a method for fatigue life analysis based on finite element results. From 1989 on he was in charge of vehicle simulation, fatigue and vibration analysis; in 1995, he became head of the engineering department. In 1999, Dr. Eichlseder was appointed Full Professor of Mechanical Engineering at the University of Leoben and head of the Chair of Mechanical Engineering. His research activities concentrate on fatigue and tribology. Since 2002 he has also been chairing the Christian Doppler Laboratory for Fatigue Analysis in Leoben.
Eichlseder, W.: Fatigue analysis by local stress concept based on finite element results, Computers & Structures (Pergamon Press), 80. (2002), p. 2109-2113 Minichmayr, R., Riedler, M., Eichlseder, W.: Thermo-mechanical fatigue testing: Methods of conducting tests and measuring the material behaviour, Archive of Mechanical Engineering, Vol. LII (2005) 4, pp. 341-351.
Eugenio Brusa (None)
Francesco De Bona (None)
Wilfried Eichlseder (None)
I. Local stress concept II. Transferability specimen – components II.1 Notches, notch sensitivity II.2 Size effect III. Influences of manufacturing on fatigue life III.1 Forming III.2 Casting III.3 Heat treatments III.4 Welding III.5 Shot peening IV. Low Cycle Fatigue (LCF) and Thermo-Mechanical Fatigue (TMF) IV.1 Influences on Thermo-Mechanical Fatigue IV.2 Simulation methods for fatigue life assessment V. Lifetime assessment of components – examples V.1 Topology optimizationGianfranco Marconi (None)
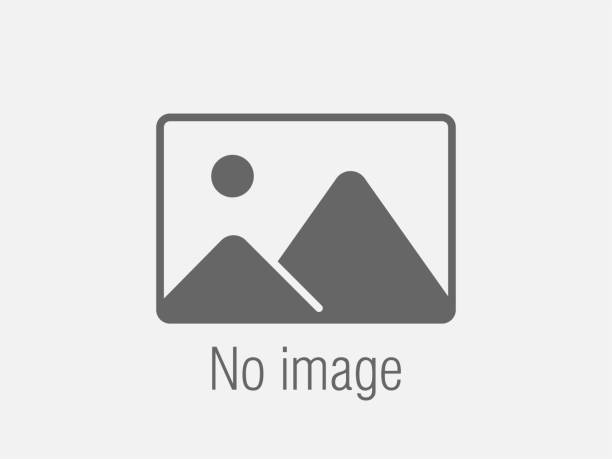